Organizations are constantly striving to optimize their operations and maximize profitability. One key aspect that plays a crucial role in achieving these goals is cost efficiency. By understanding and implementing cost efficiency metrics, businesses can identify areas of improvement, enhance productivity, and ultimately increase their bottom line.

Understanding the Concept of Cost Efficiency
Cost efficiency refers to the ability of a business to minimize its expenses while maintaining or improving the quality of its products or services. It involves finding the most efficient and cost-effective ways to achieve organizational objectives. A company that successfully implements cost efficiency practices can gain a competitive advantage by offering high-quality products or services at a lower cost than its competitors.
When it comes to cost efficiency, it is not just about cutting costs without considering the impact on quality. It is about finding the right balance between cost reduction and maintaining or enhancing the value delivered to customers. This requires a deep understanding of the business processes, supply chain management, and the overall value proposition of the company.
One way businesses can achieve cost efficiency is by leveraging technology. By automating repetitive tasks and optimizing workflows, companies can reduce labor costs and improve productivity. For example, implementing an enterprise resource planning (ERP) system can streamline various processes, such as inventory management, purchasing, and financial reporting, leading to cost savings and improved efficiency.
Definition and Importance of Cost Efficiency
Cost efficiency can be defined as the ratio of outputs achieved to the inputs used in a particular process or operation. It is an essential metric for businesses to monitor and improve upon. By analyzing the cost efficiency of different processes and operations, companies can identify areas of improvement and implement strategies to reduce costs.
Cost efficiency is important for businesses for several reasons. Firstly, it directly impacts their profitability. By reducing costs, companies can increase their profit margins and improve their financial performance. This, in turn, allows businesses to invest in research and development, expand their operations, or offer competitive pricing to attract more customers.
Moreover, cost efficiency allows businesses to allocate resources effectively, ensuring that they are utilized in the most productive and sustainable manner. By optimizing resource allocation, companies can avoid wastage and maximize the value generated from their available resources. This not only improves the overall efficiency of the organization but also contributes to environmental sustainability.
The Role of Cost Efficiency in Business Management
Cost efficiency is a vital aspect of effective business management. It enables organizations to identify inefficiencies, streamline processes, and eliminate wasteful practices. By implementing cost efficiency measures, companies can optimize their operations, enhance productivity, and achieve sustainable growth.

Furthermore, cost efficiency metrics provide valuable insights that can help managers make informed decisions and allocate resources strategically. By analyzing cost data, managers can identify trends, patterns, and areas of improvement. This allows them to make data-driven decisions that have a positive impact on the organization’s financial performance.
Effective cost efficiency management requires a proactive approach. It involves continuously monitoring and evaluating processes, identifying opportunities for improvement, and implementing appropriate strategies. This may involve renegotiating contracts with suppliers, adopting lean manufacturing principles, or investing in employee training and development to enhance skills and productivity.
In conclusion, cost efficiency is a critical factor for businesses to achieve sustainable growth and maintain a competitive edge. By focusing on cost reduction without compromising quality, leveraging technology, and implementing effective management strategies, companies can optimize their operations, improve profitability, and create long-term value for their stakeholders.
Unlock Efficiency with Teamhub
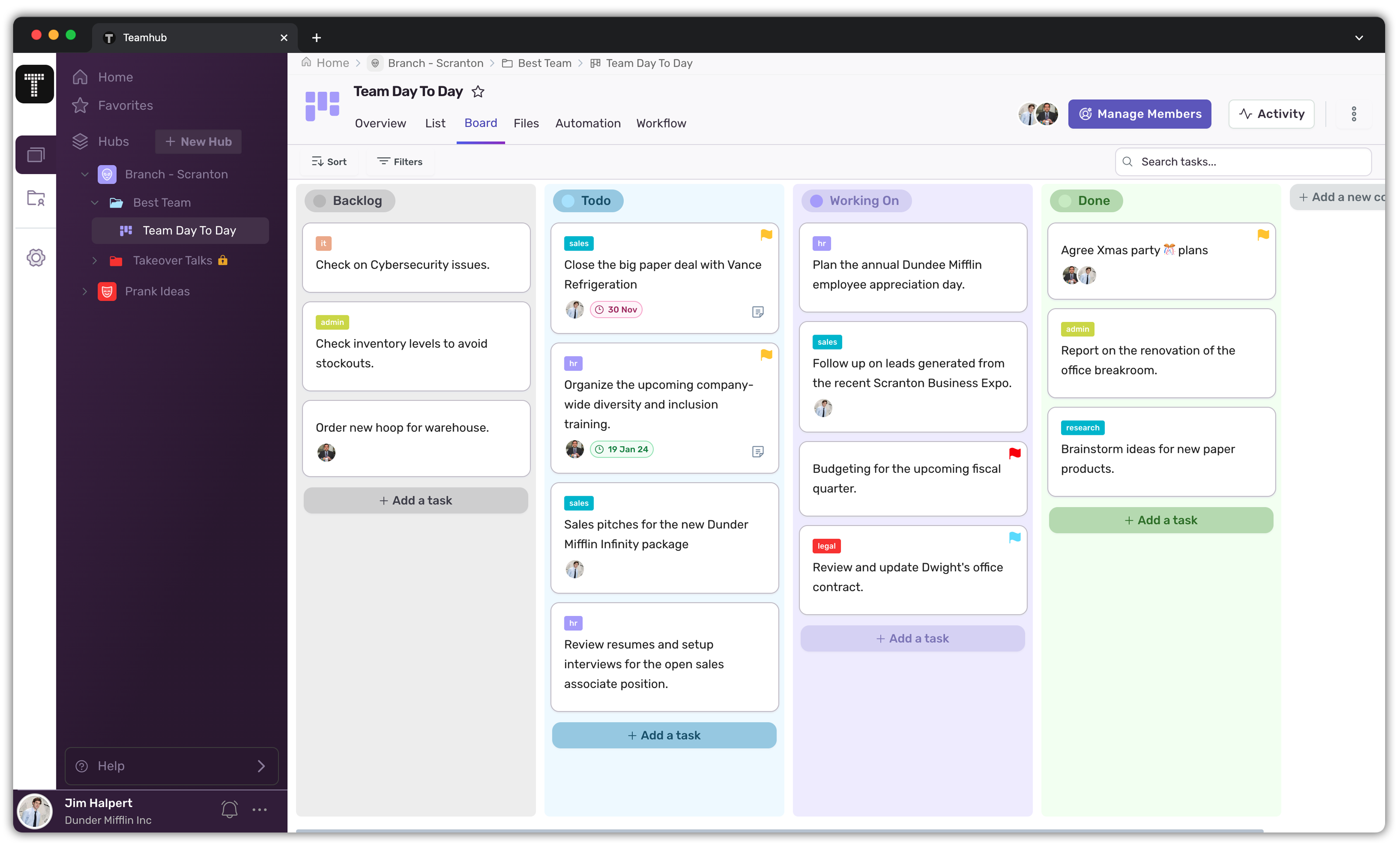
Different Types of Cost Efficiency Metrics
There are various types of cost efficiency metrics that businesses can utilize to evaluate their performance and identify areas for improvement. These metrics can be broadly categorized into two main types: direct and indirect cost efficiency metrics.
Direct Cost Efficiency Metrics
Direct cost efficiency metrics focus on quantifying the efficiency of resources directly related to the production process. These metrics assess factors such as labor productivity, material usage, and equipment utilization. By analyzing direct cost efficiency metrics, organizations can identify opportunities to reduce waste, minimize production errors, and optimize resource allocation.
For example, labor productivity metrics measure the output generated by each employee within a given time frame. By comparing the productivity of different employees or teams, businesses can identify high-performing individuals or areas that require additional training or support. Similarly, material usage metrics track the amount of raw materials consumed per unit of output. By monitoring material usage, businesses can identify potential areas of waste or inefficiency in the production process and take steps to optimize resource utilization.
Furthermore, equipment utilization metrics help businesses assess the efficiency of their machinery and equipment. By analyzing factors such as downtime, idle time, and overall equipment effectiveness (OEE), organizations can identify opportunities to improve equipment utilization, reduce maintenance costs, and increase overall productivity.
Indirect Cost Efficiency Metrics
On the other hand, indirect cost efficiency metrics measure the efficiency of resources that support and enable the production process. These metrics include overhead costs, administrative expenses, and other indirect costs associated with operations. Monitoring indirect cost efficiency metrics helps businesses identify areas of inefficiency, streamline administrative processes, and reduce unnecessary expenses.
One example of an indirect cost efficiency metric is overhead cost as a percentage of revenue. This metric calculates the proportion of revenue that is allocated to cover indirect costs such as rent, utilities, and insurance. By monitoring this metric over time, businesses can identify trends and take actions to reduce overhead costs, such as renegotiating lease agreements or implementing energy-saving initiatives.
Administrative expenses, another type of indirect cost efficiency metric, measure the cost of supporting functions such as finance, human resources, and IT. By analyzing administrative expenses, businesses can identify opportunities to streamline processes, automate tasks, and reduce unnecessary administrative overhead.
Additionally, businesses can track other indirect cost efficiency metrics such as inventory carrying costs, which measure the expenses associated with holding inventory, and supply chain costs, which assess the efficiency of the procurement and distribution processes. By monitoring these metrics, organizations can identify areas for improvement, optimize inventory levels, and reduce supply chain costs.
In conclusion, both direct and indirect cost efficiency metrics play a crucial role in helping businesses evaluate their performance and identify areas for improvement. By analyzing these metrics and taking appropriate actions, organizations can enhance their cost efficiency, increase profitability, and gain a competitive edge in the market.
How to Calculate Cost Efficiency Metrics
Calculating cost efficiency metrics involves a systematic approach that depends on the type of metric being evaluated. Let’s take a closer look at the steps involved in calculating direct and indirect cost efficiency metrics.
Steps in Calculating Direct Cost Efficiency
1. Define the inputs and outputs: Identify the specific resources and outputs that will be used to evaluate cost efficiency. This may include labor hours, raw materials, and finished products.
2. Collect data: Gather accurate and relevant data related to the inputs and outputs identified in the previous step.
3. Calculate the ratio: Divide the outputs achieved by the inputs used to obtain the cost efficiency ratio. For example, the ratio can be calculated as output/inputs.
4. Analyze the results: Interpret the calculated ratio and compare it with industry benchmarks or previous performance to assess the level of cost efficiency.
Methods for Calculating Indirect Cost Efficiency
Calculating indirect cost efficiency metrics can be a bit more complex due to the nature of indirect costs. However, there are several methods that businesses can utilize to evaluate their performance in this area:

- Activity-based costing: This method involves identifying and allocating indirect costs to specific activities or processes. By accurately attributing costs, businesses can gain insights into the efficiency of different activities and make informed decisions for improvement.
- Cost driver analysis: Cost driver analysis helps identify the key factors that drive indirect costs. By understanding the relationship between cost drivers and expenses, organizations can prioritize efforts to reduce costs and enhance overall efficiency.
- Benchmarking: Benchmarking allows businesses to compare their performance with industry peers or best practices. It provides a reference point for assessing indirect cost efficiency and identifying areas of improvement.
Interpreting Cost Efficiency Metrics
Once the cost efficiency metrics have been calculated, it is essential to interpret the results accurately to derive meaningful insights.
Understanding the Results of Cost Efficiency Calculations
Interpreting cost efficiency calculations involves comparing the obtained ratio with industry benchmarks or previous performance. If the ratio is higher than the benchmark, it indicates a higher level of cost efficiency. Conversely, a lower ratio might indicate potential areas for further improvement.
Making Decisions Based on Cost Efficiency Metrics
Cost efficiency metrics provide valuable information that can guide decision-making processes. Businesses can use these metrics to identify inefficiencies, prioritize improvement initiatives, and allocate resources effectively. For example, if a particular process or activity is identified as inefficient, management can explore strategies to streamline operations, reduce costs, and enhance overall efficiency.
Improving Cost Efficiency Metrics in Your Business
Enhancing cost efficiency is an ongoing process that requires continuous evaluation and improvement. Here are some strategies and techniques that businesses can employ to boost their cost efficiency metrics:
Strategies for Enhancing Direct Cost Efficiency
1. Implement lean manufacturing principles: Lean manufacturing focuses on minimizing waste, optimizing resource utilization, and improving overall efficiency. By adopting lean practices, businesses can identify bottlenecks, reduce cycle times, and enhance direct cost efficiency.
2. Automate processes: Automation can help streamline operations, improve accuracy, and reduce costs associated with manual labor. By automating repetitive tasks, businesses can free up resources for more value-added activities.
3. Train and empower employees: Investing in employee training and development can result in a skilled and dedicated workforce. Well-trained employees are more likely to perform tasks efficiently and contribute to achieving cost efficiency goals.
Techniques for Boosting Indirect Cost Efficiency
1. Review and renegotiate contracts: Regularly assessing contracts with suppliers, service providers, and vendors can help identify cost-saving opportunities and renegotiate terms to achieve better pricing.
2. Implement cost control measures: By implementing effective expense management strategies, businesses can monitor and control indirect costs more efficiently. This may include implementing cost control policies, expense tracking tools, and regular performance reviews.
3. Embrace technology solutions: Technology can play a significant role in improving indirect cost efficiency.
By incorporating cost efficiency metrics into their business operations, organizations can gain valuable insights into their performance, identify areas for improvement, and make informed decisions. By continuously monitoring and enhancing cost efficiency, businesses can achieve sustainable growth, remain competitive, and thrive in today’s dynamic marketplace.
One thought on “Cost Efficiency Metrics Explained”